A guide to cryogenic materials testing for electric and hydrogen aircraft
Although exact definitions vary, cryogenic temperatures are generally defined as occurring between around 120K (-153˚C) and absolute zero (0K, or -273˚C).
Historically, materials testing in this temperature range has related to cryogenic fluids such as Liquefied Natural Gas (LNG) and liquid helium. However, as a growing number of companies explore the development of electric and hydrogen-powered aircraft, engineers must learn how to deal with and test superconducting materials and high-pressure systems for the storage of hydrogen at cryogenic temperatures down to -200˚C.
Cryogenic testing caters for the characterization of all aircraft components exposed to cryogenic conditions and seeks to deepen the understanding of how these low temperatures change their performance, including their mechanical and electrical properties.
According to Jill Miscandlon, senior manufacturing engineer at the Advanced Forming Research Centre at the National Manufacturing Institute Scotland (NMIS), cryogenic testing requires the use of equipment including helium gas circulation systems and cryogenic propulsion test units. Such facilities are currently being developed as part of a purpose-built laboratory at the University of Strathclyde, Scotland.
Table 1: Hydrogen and electric aircraft parts that need to be cryogenically testedType of PartLiquid hydrogen tanksLiquid hydrogen transfer lines, flexible/rigid linesPump designsPower electronic elements like inverters and otherControl elements and valvesLiquid hydrogen tank insulation testingHeat flux measurements through insulation materialsBoil-off measurementsEffective thermal conductivity (ke) measurements depending on tank insulation qualityResidual gas measurements in vacuum environmentDetection of oxygen formation on surfacesSource: Wolfgang Stautner, principal engineer at GE Global Research
Miscandlon points out that the use of liquid hydrogen as an aircraft fuel also requires the cryogenic testing of many parts, including tanks, pipes, pumps, valves, sensors, sealing technologies and heat exchangers. The development of hydrogen propulsion systems also requires the testing of power cables, machine drives and electrical machines in cryogenic environments. “Until now, testing has been undertaken on active components. There is a requirement for the development of non-active component testing in cryogenic environments to understand if the materials currently being used will cope in cryogenic systems. If materials are evaluated as insufficient, new materials will be required,” says Miscandlon.
Types of testing
Although the broader cryogenic range applies to temperatures in the 0-120K range, Wolfgang Stautner, principal engineer at GE Global Research points out that the cryogenic environment used to be considered to start at temperatures below 77K.
However, with the arrival of cryogenic designs and applications for LNG, Stautner says there are “efforts in the cryogenic community to move the boundary up to above 111K”.
Tests at cryogenic temperatures refer to the measurement of the physical and mechanical properties of metals, composite structures or combinations of the two. In this case, physical properties include thermal conductivity and shrinkage and mechanical properties include Young’s modulus –the capability of a material to withstand changes in length when subjected to lengthwise tension or compression – and UTS (Ultimate Tensile Strength).
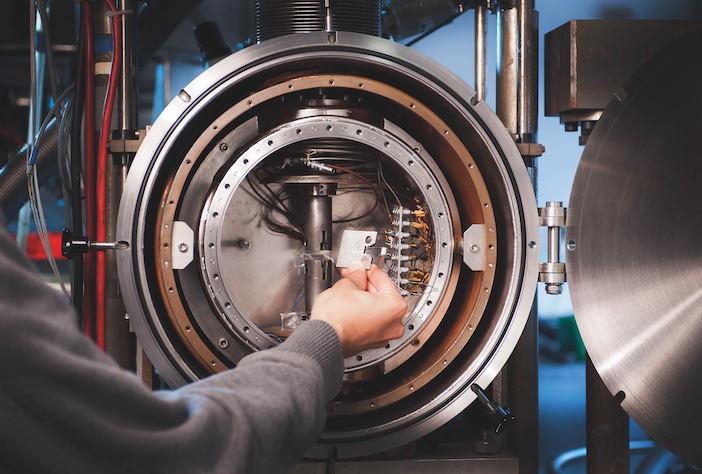
“Many tests can be executed at LN2 temperatures at 77K, but materials exposed to liquid hydrogen at 20K can show different material properties and really need to be tested in a liquid hydrogen environment to be conclusive,” says Stautner.
When it comes to hydrogen and electric aircraft, Stautner reveals that a wide range of parts will need to be tested cryogenically (see Table 1).
Technical challenges
According to Mike Sumption, professor of materials science and engineering at Ohio State University, the key challenges relating to the use of cryogenics are thermal management, safety, materials costs, standards and reliability.
“Technical challenges include those related to cost reduction, the development of cryogenically insulating but thermally conductive materials and high performance, low loss, conductors,” he says.
For Stautner, the most likely challenges moving forward include those related to reliable hydrogen pump design and the “cavitation and embrittlement of metals” – as well as to the availability of hydrogen fuel at airports.
Meanwhile, Jacob Leachman, associate professor in the School of Mechanical and Materials Engineering at Washington State University points out that although liquid hydrogen has the highest combination of energy density and specific energy of any fuel, the heaviness of the fuel tank it is stored in creates a challenge in aviation applications. Moreover, although novel 3D-printed materials have substantially higher specific strength than traditional metallic containers, he warns that material characterization is yet to be done to understand the behavior of these materials at cryogenic temperatures.
“The key challenge for liquid hydrogen aircraft is the need for lightweight storage vessels and transfer lines with little to no boil-off,” he says. “The testing of such vessels is very challenging due to the need to create or procure liquid hydrogen and the need to vent hydrogen through a vent stack.
“Little to no research has been done in this area for several decades and there is now a plethora of manufacturing methods and materials available. Only recently have federal program managers in the US noticed this need, but not soon enough to help the people pioneering in this new sector,” he adds.
Glacial progress
Although Leachman believes that the body of knowledge relating to traditional stainless steel or aluminium liquid hydrogen vessels is adequate, knowledge about everything else is inadequate. Even so, he is confident that new materials with novel manufacturing methods can create tank geometries with integrated heat exchange functions that solve many of the traditional challenges.
“We recently showed that compliant fuel bladders are possible with liquid hydrogen. It is now possible with a cryocooler, cryostat, and a good hydrogen safety plan to conveniently liquefy and test materials in hydrogen at universities. That should get the field moving,” says Leachman.
Broadly speaking, Stautner believes that the body of research relating to cryogenic materials and testing has been progressing at a very slow pace for the last 60 years.
“The only input is from accelerator magnets and superconducting magnet technology. We basically use data generated on materials in the 4K and 20K temperature range that were generated many years ago – and for materials available at that time. We do not know the physical nor mechanical properties of materials developed more recently. We are in very bad shape, in this area” says Stautner.
“These tests are expensive and need a certain amount of care when carried out to ensure data is correct and applicable. There are only a very few cryogenic test sites in the world, for example at the Karlsruhe Institute of Technology or Saclay. We need experts that would like to work in this field,” he adds.
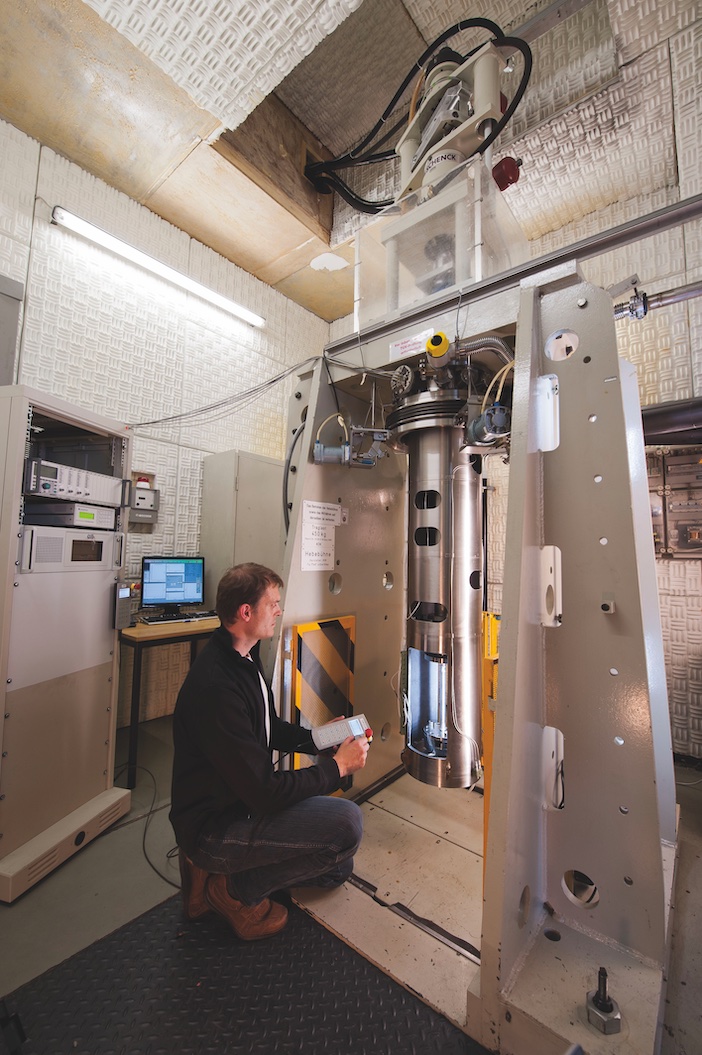
Although additive manufacturing will move into aerospace technology for cryogenic applications, Stautner stresses that extensive material property testing will be mandatory. “Research is needed on tank materials for cryogenic use, the development of a catalogue of fatigue properties for composites, ceramics and other novel materials, and the development of new materials for zero hydrogen diffusion, including liner designs or liner-less designs,” he says. “The industry must also develop liquid hydrogen pumps that work reliably without cavitation and vacuum-jacketed lightweight transfer lines for use with liquid and gaseous hydrogen. We also need to continue to develop and shape liquid hydrogen powered aircraft safety standards that are impossible to generate without materials testing – including hydrogen embrittlement studies.”
A complete solution
Elsewhere, Gladys Benghalia, strategic coordinator – Net Zero: Electrification at NMIS stresses that the knowledge required to fully understand the operational capabilities of materials can be vast. “A fundamental understanding of the thermal gradients and cycles of the application is required. Applicability of the materials in question requires thorough and in-depth testing and characterization procedures to allow us to successfully implement new materials for hybrid and electric aircraft applications,” she says.
If materials are deemed unsuitable, Miscandlon points out that material development programs will be required to optimize performance – a task she describes as “a large undertaking to achieve for hybrid / electric flight in the timeframes intimated.”
“At the University of Strathclyde, collaborations in electrical, mechanical and manufacturing expertise are in focus to allow an all-encompassing solution for the benefit of our industrial partners to provide the most efficient route to design, manufacture and operation,” she says.
“It is clear that there is a huge body of work required, reflected in the TRL expectations in Horizon Europe funding calls, for example, where a target of TRL 4 is being targeted by 2030,” she adds.
The life-cycle approach to future propulsion
The use of cryogenics in future aircraft is being explored at the University of Strathclyde’s Applied Superconductivity Laboratory. There are complex cooling requirements for all aspects of cryogenic propulsion systems, including auxiliary items and storage tanks.
Gladys Benghalia, strategic coordinator – Net Zero: Electrification at National Manufacturing Institute Scotland (NMIS) says, “Cryogenic propulsion systems by their very nature hold many complexities in comparison to traditional combustion engines. In considering the optimization of the system a holistic approach is being adopted to use the varying temperatures in different regions of the system.
“This can be exploited by transferring the cooling from one region of the system to be used in another region, thereby creating a fully optimized system and further contributing to the lightweight and sustainable nature of the system,” she adds.
Benghalia believes that lessons can be learnt from gas turbines, where there are detailed, intricate MRO procedures. If MRO is not considered during the design stage, maintenance can become very costly and time consuming for cryogenic propulsion systems.
Learning from gas turbines is being incorporated into the sustainable manufacturing focus at NMIS through the Future Electrical Machines Manufacturing Hub, which has the key aim of enabling the future design and operation of machines including life cycle requirements at the design stage.
Ensuring safe cryogenic testing
Cryogenic fluids, which are also known as cryogens, and the facilities that handle them are subject to additional safety considerations because of several factors. These range from the potential for asphyxiation or frost bite burn for handlers to the risks associated with large expansion ratios during heating to room temperature that can burst most containers.
There are two common ways of achieving cryogenic temperatures, one is to use cryogenic liquids or gasses to cool materials directly, the other is to use a refrigeration technique not unlike conventional refrigeration – where gas is compressed on the hot end and expanded in areas where users want it to cool, but with a gas such as helium.
In the first case, liquid-containing dewars are used to contain the liquid. In the latter the test piece is put in a vacuum enclosure to thermally isolate it and then cooled by conduction from cryogenic refrigerator cold heads.
“All of the standard safety considerations apply but in addition safety aspects for inert cryogenic liquids include frostbite and asphyxiation due to liquid to gas phase change in enclosed spaces. If hydrogen is used, its flammability hazards must also be taken care of,” says Mike Sumption, from Ohio State University.